Un material limpio, fuerte y bonito
Como explica Guillaume Beuvelot, director de ventas de Cobratex, la empresa se creó para hacer un diseño ecológico y hacer que los materiales compuestos sean menos grises y más verdes. Tras 6 años de observación del mercado, su fundador, el ingeniero Edouard Sherwood, lanzó Cobratex en 2013 para desarrollar el uso del bambú en materiales compuestos. tres veces más ligero que la fibra de vidrio, con una densidad de entre 0,7 y 0,9, el bambú tiene unas características mecánicas equivalentes a la vez que es más respetuoso con el medio ambiente y estético.
Un proceso patentado
Gracias a numerosos proyectos de colaboración y a la I+D de Cobratex, la empresa ha desarrollado un proceso de fabricación patentado que es totalmente mecánico, lo que hace que consuma menos energía y preserve las propiedades mecánicas del material. Una línea de producción piloto de 9 máquinas lleva a cabo las principales etapas. El bambú se "pela" y las fibras se clasifican según sus características. A continuación, se reúnen en tiras de 2 a 5 mm de ancho de 1/10 e à 3/10 e de grosor. Por último, los tejedores los unen para obtener tejidos que se utilizan habitualmente en la industria de los compuestos.
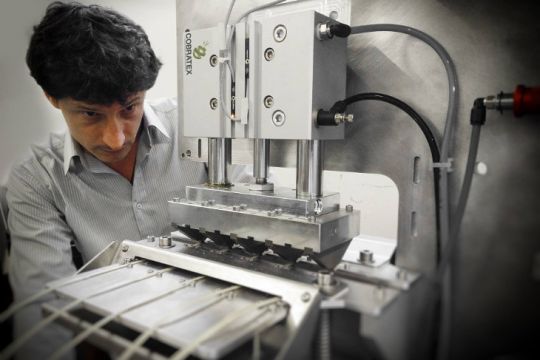
Los tejidos resultantes pueden utilizarse con cualquier tipo de resina de poliéster, viniléster o epoxi. Actualmente se están realizando pruebas para validar el proceso según las distintas aplicaciones industriales.
Primeros manifestantes
Desde que se produjeron los primeros tejidos Cobratex, se han producido los primeros demostradores en varias industrias de transporte. En el JEC World 2017 se expuso una aleta de Cobratex y se espera que la primera tabla de surf con este material salga a la venta en breve.
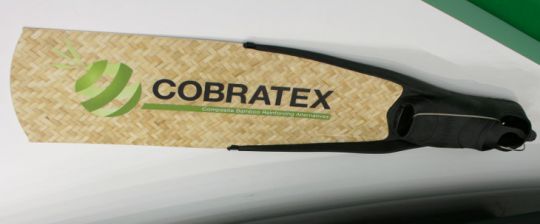
La empresa está recaudando fondos para industrializar la producción y continuar la I+D para caracterizar mejor los materiales.
Interés en el sector náutico
Cobratex estuvo presente en reuniones profesionales y pudo calibrar el interés de la industria náutica. Los tejidos de bambú deberían poder utilizarse pronto para el acondicionamiento interior y el mobiliario de los barcos. En una segunda fase podría desarrollarse un uso estructural, mientras se realizan pruebas con la asociación EcoTransat.